Want to go from theory to practice?
Try MDCplus for freeMachine Downtime Tracking Software Explained
Behind The Curtain of Machine Downtime Tracking Software
Minimizing machine downtime is a critical priority for maintaining efficiency and competitiveness in manufacturing environments. Downtime tracking software, powered by real-time data, offers a comprehensive tool for monitoring equipment performance, improving production schedules, and optimizing overall productivity. These modern extensions empower manufacturers with actionable insights, enabling faster responses and more effective planning.
Understanding Downtime Tracking
Machine downtime refers to periods when equipment is non-operational, causing disruptions, reduced output, and financial losses, especially costly when it's 5-axis CNC is not operated enough time. Effective downtime tracking provides clarity on these interruptions, helping businesses identify inefficiencies, schedule preventive maintenance, and allocate resources effectively. Traditional manual tracking methods often fall short in providing timely and accurate insights. Real-time downtime tracking software eliminates these shortcomings by collecting live machine data, offering immediate visibility into performance and productivity. Of course, starting off with tracking machine downtime using EXCEL spreadsheet may seems easier, but make sure you are the downtime cause yourself with manual data collection.
The Importance of Real-Time Data
Real-time data transforms downtime tracking from a reactive process to a proactive strategy. With instant updates, manufacturers can quickly identify bottlenecks, prevent recurring issues, and address stoppages before they escalate. This level of responsiveness improves operational efficiency, enhances maintenance planning, and reduces the risk of unexpected disruptions.
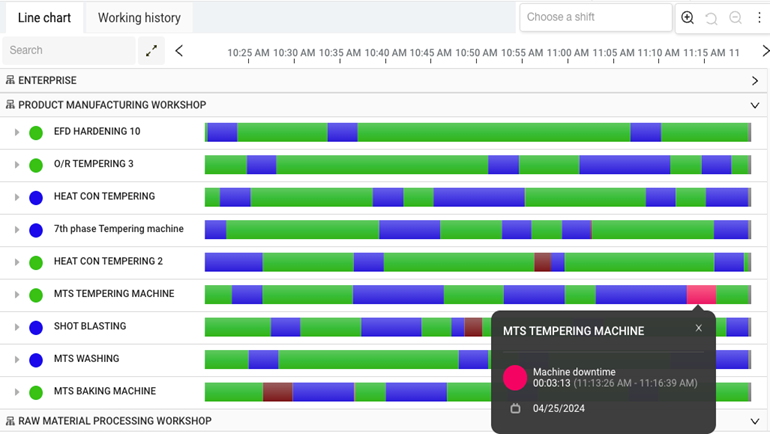
Key Features of Downtime Tracking Software
Downtime tracking software is equipped with features designed to maximize equipment efficiency and streamline production workflows:
- Live Monitoring: Provides a real-time view of machine performance and OEE, allowing for immediate identification of problems.
- Detailed Reporting: Offers insights into downtime causes, frequency, and duration to prioritize improvements.
- Predictive Maintenance: Uses data trends to anticipate and prevent potential equipment failures.
- Custom Dashboards: Allows businesses to tailor software interfaces to their specific needs for better data accessibility.
- Scalability: Accommodates operations of all sizes, from small workshops to multinational facilities.
Benefits of Real-Time Downtime Tracking
Implementing downtime tracking software delivers substantial benefits for manufacturing operations:
- Cost Reduction: By identifying inefficiencies, businesses can minimize maintenance costs, reduce waste, and avoid unplanned shutdowns.
- Increased Productivity: Real-time insights enable faster response times, ensuring equipment operates at peak performance.
- Improved Resource Allocation: Data-driven insights help optimize labor, materials, and machine usage, improving overall workflow efficiency.
- Maintenance Optimization: With predictive tools, manufacturers can transition to condition-based maintenance, reducing unnecessary servicing while avoiding unexpected breakdowns.
- Enhanced Decision-Making: Detailed analytics provide a foundation for strategic planning, such as equipment upgrades, production line adjustments, or workforce deployment.
- Compliance and Reporting: Comprehensive monitoring supports adherence to industry standards and simplifies regulatory reporting.
- Sustainability: Tracking energy consumption and optimizing machine use contributes to greener operations and reduced environmental impact.
How MDCplus Reduce Downtimes
MDCplus is designed to tackle the challenges of machine downtime heads-on, combining advanced technology with practical tools to enhance operational efficiency. By leveraging real-time data, MDCplus provides manufacturers with the insights and capabilities needed to minimize interruptions and optimize performance across production lines.
Real-Time Monitoring and Alerts
Direct integration with equipment with live updates on machine performance and notification system
Preventive Maintenance
Identifying failure points, reduces unexpected downtimes and extends machine lifespan
Comprehensive Reporting
Create insights on inefficiencies to implement targeted improvements, real-time and historically
Customizable Dashboards
Display the most relevant metrics for your operations to ensure the clarity of processes
About MDCplus
Our key features are real-time machine monitoring for swift issue resolution, power consumption tracking to promote sustainability, computerized maintenance management to reduce downtime, and vibration diagnostics for predictive maintenance. MDCplus's solutions are tailored for diverse industries, including aerospace, automotive, precision machining, and heavy industry. By delivering actionable insights and fostering seamless integration, we empower manufacturers to boost Overall Equipment Effectiveness (OEE), reduce operational costs, and achieve sustainable growth along with future planning.
Ready to increase your OEE, get clearer vision of your shop floor, and predict sustainably?