Get your CNC monitoring done right
Start a project with MDCplusCNC Machine Monitoring Software
Manufacturing today is a high-stakes game where efficiency and precision determine success. For shop floor workers and supervisors, CNC machine monitoring software offers a practical, highly effective tool to manage operations efficiently. By transforming data into actionable insights, these tools minimize downtime, optimize workflows, and create a more efficient workplace.
Why CNC Machine Monitoring Software is Essential
CNC machine monitoring software stands out because it’s built for the realities of the shop floor. Here’s what makes CNC machine monitoring software essential:
- Automated Data Tracking: No more manual logs. These systems track spindle speeds, tool usage, cycle times, and even error codes, giving teams accurate, up-to-date information without the hassle.
- Direct Connections to Equipment: Many monitoring systems connect directly to leading CNC controllers such as FANUC, HAAS, and Siemens, ensuring comprehensive data capture without extra hardware.
- Clear Dashboards: Think of it as a central dashboard—real-time visualizations make it easy to see what’s happening and where attention is needed.
- Alerts That Matter: Early warnings about tool wear or overheating let teams fix problems before they escalate, saving valuable time and money.
- Analytics for the Long Game: Beyond daily operations, these tools provide insights into machine utilization, downtime trends, and OEE, helping manufacturers strategize for the future.
Make CNC Monitoring Your Tool
All KPIs, including OEE calculation
MDCplus has a centralized dashboard for key performance indicators, an NC execution journal for detailed process tracking, and a user-friendly worker tablet interface. These features provide a clear view of operations, ensuring every operator has instant access to actionable insights. By streamlining communication, reducing downtime, and enhancing productivity, this software empowers manufacturing teams to maintain higher levels of efficiency and consistency across all CNC machining tasks.
Practical Benefits of CNC Monitoring Software
Real Cases = Success Stories
Monitoring solutions don’t just promise results - they deliver.
Consider Komax Belgium, a leading wire processing company that revolutionized its production with the help of CNC monitoring software. By integrating these tools, Komax improved machine utilization by over 20%, ensuring timely order fulfillment and reducing downtime significantly. To learn more and dive into the details, dive here to read MDCplus success story with KOMAX.
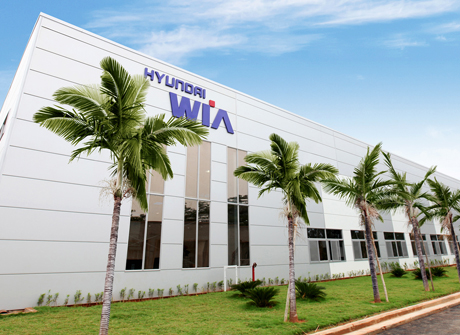
Another success story comes from Hyundai's partnership with MDCplus. Hyundai leveraged monitoring systems to enhance their assembly line efficiency, achieving a remarkable reduction in operational bottlenecks and improving overall equipment effectiveness.
For workers and supervisors, the value of machine monitoring software is immediate and practical:
- Instant Visibility: Know the status of every machine in real-time, eliminating the guesswork that slows down operations.
- Fewer Breakdowns: With maintenance features, potential issues are caught early, keeping machines running longer and reducing costly repairs.
- Focus on What Matters: Workers can prioritize critical tasks instead of being bogged down by routine inspections or troubleshooting.
- Better Team Coordination: Centralized data ensures everyone is on the same page, making it easier to collaborate and solve problems.
Solving the Big Challenges
These real-world examples demonstrate how CNC monitoring software not only addresses pain points but also delivers tangible benefits that improve day-to-day manufacturing processes.
Manufacturing isn’t without its pain points, and CNC machine monitoring software addresses some of the toughest challenges:
- Unplanned Downtime: Early detection systems help avoid the expensive ripple effects of unexpected machine failures.
- Underperformance: Real-time tracking ensures machines are being used to their full capacity, eliminating inefficiencies.
- Information Overload: Simplified dashboards cut through the noise, presenting only the most critical data for quick decision-making.
Why It Matters
CNC monitoring software goes beyond simplifying shop floor management; it elevates operational efficiency to new levels. By equipping workers and supervisors with timely, accurate information, these systems enable swift, confident decision-making that drives productivity and ensures high-quality output. In a manufacturing landscape where precision and efficiency are paramount, adopting CNC machine monitoring software is a great way to optimize your shop floor operations.
For manufacturers aiming to stay competitive, machine monitoring software is the ultimate ally. It’s about more than tracking performance; it’s about unlocking the potential of every machine and every worker on the floor. By incorporating advanced features and direct connectivity to FANUC and HAAS controllers, and complex analytics, these systems will continue to shape the future of manufacturing, enhancing efficiency and fostering improvement.
About MDCplus
Our key features are real-time machine monitoring for swift issue resolution, power consumption tracking to promote sustainability, computerized maintenance management to reduce downtime, and vibration diagnostics for maintenance. MDCplus's solutions are tailored for diverse industries, including aerospace, automotive, precision machining, and heavy industry. By delivering actionable insights and fostering seamless integration, we empower manufacturers to boost Overall Equipment Effectiveness (OEE), reduce operational costs, and achieve sustainable growth along with future planning.
Ready to increase your OEE, get clearer vision of your shop floor, and predict sustainably?